How Lean transforms relationships to empower employees and increase impact
DOI :
https://doi.org/10.21153/thl2021art1495Mots-clés :
humanitarian, leadership, private sector, LeanRésumé
The challenges of humanitarian leadership are well-studied by the social sciences. However, there is untapped potential in applying private sector management principles and best practices to humanitarian work. Some non- profit organisations have fruitful experience applying Lean Management, an innovative management system developed by Toyota, which is not just about manufacturing better cars or improving industrial processes. Lean focuses the organisation on providing more value to its customers which, in the case of the humanitarian sector, are its beneficiaries. Our panel shared their experience of using Lean Management to address common issues in humanitarian operations. Their stories demonstrate the potential of Lean to transform work and relationships by devolving power to lower-level workers and partners. By empowering staff and local entities, it also improves relationships, collaboration, and ultimately the outcomes of humanitarian missions.
Métriques
Téléchargements
Références
Akers, P. A. (2016). 2 Second Lean: How to Grow People and Build a Fun Lean Culture. BookBaby. https://paulakers.net/books/2-second-lean
Garvin, D. A. (1993). Building a learning organization. Harvard Business Review, 71(4) 78-91.
Girardin, C. (2021). Evaluating the Promotion of Innovation in NGOs. HUMLOG blog. https://blogs.hanken.fi/humlog/2021/07/28/evaluating-the-promotion-of-innovation-in-ngos/
Netland, T. H., & Powell, D. J. (Eds.). (2016). The Routledge companion to Lean Management. Taylor & Francis.
Parris, A. (2013). Improving processes for good in East Africa The TQM Journal. 25(5) 458-472. https://www.wvi.org/sites/default/files/Improving%20processes%20for%20good%20in%20East%20Africa.Final%20to%20share.2013-08-29.pdf or https://www.linkedin.com/in/andrew-parris-0b4ab28/detail/overlay-view/urn:li:fsd_profileTreasuryMedia:(ACoAAAGWAQgBKTHUCM40mDiR7bcb4tIDLMaoOsc,1554731606281)/.
Parris, A. (2019). Making work and the world a better place. ISE Magazine 51(4) https://www.linkedin.com/in/andrew-parris-0b4ab28/detail/overlay-view/urn:li:fsd_profileTreasuryMedia:(ACoAAAGWAQgBKTHUCM40mDiR7bcb4tIDLMaoOsc,1554730618048)/.
Parris, A., Pope, D. (2020). What Christian Leaders Can Learn From Lean. Management Sciences. 21. https://digitalcommons.acu.edu/mgt_sciences/21 or https://www.yumpu.com/en/document/read/64438356/christian-business-review-2020-leadership/26.
Parris, A., Thakur-Weigold, B., Wagner, S. (2021). Medair’s Beirut Blast Response 2020. unpublished teaching case study.
Taylor, D., & Pettit, S. (2009). A consideration of the relevance of lean supply chain concepts for humanitarian aid provision. International Journal of Services Technology and Management, 12(4) 430-444.
Womack, J. P., Jones, D. T., Roos, D., & Carpenter, D. S. (1991). The machine that changed the world: based on the Massachusetts Institute of Technology 5-million-dollar 5-year study on the future of the automobile. Rawson Associates.
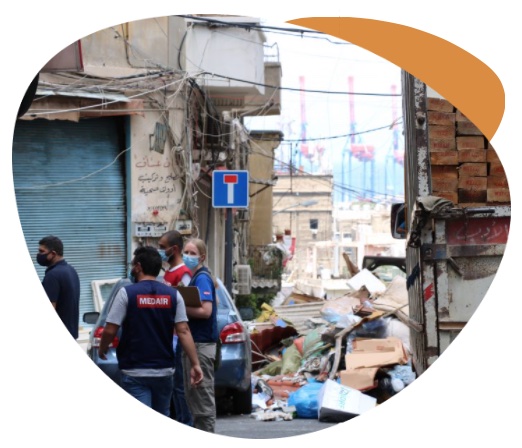